Clamshell Rooftop Tent (MK2)
- TroubleMake[r]
- Sep 11, 2021
- 7 min read
Updated: Sep 17, 2021
You know what sucks? The fact that even inexpensive rooftop tents start at about $1400. I'm pretty sure I can build one for less than half that, and I did, before this one I had my MK1 tent, a fold out one. It was awesome, but heavy, the set up was still slower than I'd like - and while it was much slimmer than a new one (5" tall folded, vs the 8-12" tall manufactured ones), it was still talker than I'd like.
Let's start by saying: this thing is awesome. It is light enough that I can lift it and put it on the car by myself, it feels awesome to be able to set up wherever I please and quickly too. All that said, it is technically not finished. I am still trying to get the thing water tight for driving. It sheds water beautifully when camping, and the sound of the rain on the roof is truly awesome, but when you get the added air pressure of driving in the rain, some water gets in.

It should also be noted that in order to even make this rooftop tent possible for my car, a 2012 Toyota Rav4, I had to fabricate a new roof rack, more on that here.
Question: Can I build a comfortable rooftop tent, that meets the vast majority of the features offered in a new one, myself and for substantially less money?
Research: There are a few people out there who are much better at this stuff who have made rooftop tents and wedge campers that were a bit overbuilt for my tastes, but incredible products. I took materials that I know and have used, and began to put something together.
I knew I needed at the very least two identical halves, a top and a bottom, mounted with some hinges, supported by gas struts, and shut with clasps or some type of locking hardware.
I would also need some outer material for the "roof" and "floor" of the tent.
The fabric part would be much easier than the one from MK1, as I would basically be making two triangles and a rectangle. Throw in some zippers, some bug netting, and some velcro, and that part would be pretty straight forward.
I'd be using hardware for the bulk of the assembly, and luckily due to the material, I only had a couple different sizes of bolts.
Preparation: Most of the tools I'd be using for this I already had, I only had to replenish the shop of a few things here and there. There's nothing exotically dangerous about the materials, so standard shop safety should suffice.
Execution: To start the design, as mentioned above, I had to build a roofrack for my car. The existing roof rack wasn't meant for something this long, and I didn't want to overburden the tent with unnecessary leverage to and fro. I only felt comfortable building the roofrack so wide, which meant I could only build the tent so wide. I decided that a comfortable footprint for me would be about 43"x76", which would give me a half inch of space on either side to fit on the roofrack, which is 44"x 81". I'm 5'10", and by myself, that size is fine, no issues. I can fit my girlfriend in there, and the space becomes limiting, but it's not uncomfortable - it's camping, afterall.
Materials & Tools: As mentioned, I didn't really use anything special for tooling, I had to buy a new M8 tap, that's it though.
Mats - (QTY) (Desc) (Length x Width x Height)
(4) 3030 2 Slot Extruded Aluminum (73.625"x30mmx30mm)
(4) 3030 4 Slot Extruded Aluminum (41.625"x30mm,30mm)
(3) 3030 Hinges w/Hardware
(2) 3mm Alupanel (76"x43"x3mm)
(2) 60lb Gas Struts (36")
(48) M6x1 Black Oxide Stainless Low Profile Button Head Bolts (12mm)
(Bag of 100) M6 Stainless Flat washers
(16) M8x1.25 Stainless Button Head Bolts (35mm)
(Bag of 100) 3030 8mm T-Nut M6x1 thread
(8) 3030 90° Gussets
(10yrds) PU Coated Canvas (36" x 60")
(4) Outdoor double pull zippers (36")
(4yrds) Noseeum Mesh (36" x 60")
(5yrds) Webbing of your choice of width
Tools -
Drill
Bit Driver
M8x1.25 tap
1/8"-5/8" Stepper Bit
Blue loctite
Deburring tool
Sewing Machine
Fabric Rotary Cutter
Lots and lots of sewing pins
Making the main structure of the tent is easy peesy lemon squeezy. I tapped the ends of the 3030 Aluminum at a depth of 40mm with an M8x1.25 tap, then threaded the bolts for same in with the gussets holding them together into rectangles. This did actually take a little bit of machining down on the button head bolts, as they interfered with each other slightly. I took each screw and put it in the collet of the drill so the bolt head was pointing out, and just drug it on some sandpaper to take away a bit of material. Once those are together, I mounted the hinges on the back, and made this a big clamshell to open and close. Keep in mind that while this strong right out of the gate, the torsional rigidity isn't quite there due to how long the sections are, so don't get too excited moving them back and forth. For the Alupanel, I bought the stuff from a sign shop and they cut the pieces to length for me to boot, so all I did was line up where the holes would go, used the stepper bit to drill 24 equally spaced holes around the edges of each panel to mount the panels to the 3030 aluminum tracks, deburred the edges of the holes, and put in the hardware (1 M6x1x12mm bolt, washer, and T-nut, then fitted the sheets to the top and bottom of the frame. These T-nuts can be a pain in the butt sometimes to tighten properly, but I decided to go with these over the sliding nuts because I didn't want to have to fish around blindly for a poorly placed nut. There is a slightly more expensive option that combines the best of both, but eh.
Once those panels are on and torqued down (I did about 7nm on each one, or just as the bolt starts to visibly compress the alupanel, the main structure is mostly done, if you can believe it. The next steps involved me measuring out the total height that I wanted the structure to be at when fully opened, which told me the overall measurements of the fabric, and where the struts needed to be. Cutting the fabric required a large space, what I did is I measured the inside of the structure where the fabric would be mounted, all the way around to get an idea of how long the piece would be. I laid out a few sheets of plywood on the floor to use as a flat cutting surface, folded the large piece of fabric in half to demonstrate the symmetry of the cut. Then I split my measurements in half, drew out where the cuts would need to be, and using a long straight edge and some clamps, cut out my shape, leaving about 2" of excess for folds.
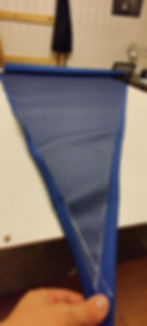
While it was there, I clarified my measurements, then I started to fold it over and use pins to hold the fabric in place for the stitching, as seen on the left side here.
This part I would definitely change if I were making a MK3 anytime soon. For starters, I should have left more fabric, and I also would have used Keder cord in order to mount the fabric to the frame.
The sewing parts of this for me are never pretty, but the gist is to try to keep the fabric fairly taught as you guide the fabric through the sewing machine, so you don't get bunched up sections. This PU Canvas was a lot more manageable than the ripstop nylon from the MK1 was.
Ultimately I ran through and gave the entire fabric a 1" fold, with two stiches across each length of fold, as seen on the right side.
I had two ideas for mounting the fabric to the frame, which I'll talk about later.
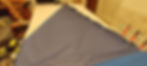
Once I got the edges hemmed, I started to temporarily mount the fabric onto the frame whilst checking the overall length. I knew I wanted openings on each side, but I was unsure how large I wanted them to be. I had lofty goals of eventually building in some hanging pockets into the PU Canvas on the inside, so I didn't want to take up all of my fabric real estate with openings and mesh. What I decided on was to use the 4 36" zippers I had left over from the MK1, and make a double zippered opening on the front of the tent, and two triangle shaped openings on each side.
I cut the flaps that would end up being the doors, and sewed in noseeum mesh panels, gave everything a 1/4" hem, and sewed on webbing and velcro at the bottom of each to hold them in place. The tops of each opening got a small piece of velcro webbing to roll it up and keep it in place.

The mounting part of the fabric is a pain. My original plan was to stamp grommets and use hardware, I found I didn't like this in theory, so my temporary solution was to use mounting hardware with two large washers to clamp the fabric between the washers all along the tracks. Surprisingly, it's still working, and allows me easy adjustments if needed.
Installing the gas struts made the whole system a working prototype, and boy was I glad about that. I had to attach some latches to hold it closed, I'm still working on this aspect, as I am not in love with these particular features. I ended up using a mixture of foam sealing tape, and silicone to waterproof it, which again, hasn't completely solved the waterproofness when driving in the rain.
At this point I was ready to at least test it, so we took it up to the mountains for a test run. We both liked it a lot, and like I mentioned, it's tight with two people.


When we got back I had an idea to use window spring rods and some tarp clamps to make an awning, so I through that together.

I also used a temporary solution to mount the tent to the rack, which has been working really well: I used some large webbing and hardware to make a heavy duty velcro strap that holds everything nicely.

All in all, this turned out to be a quick and mostly easy project that yielded some amazing results.
My total cost on this ended up being just under $400, with some minor/cheap enhancements here and there.